طراحي جوش
بحث در طراحي جوش متناوباً در بخش هاي مختلف قبلي كتاب كم و بيش آورده شده است و با تكيه بر مبناي اصولي سعي خواهد شد تا از تكرار مطالب اجتناب شود. رعايت تضمين ايمني يا ضريب اطمينان بر روي مواضع جوش داده شده ، مستلزم طراحي اتصال به طور صحيح و دقيق مي باشد . يكي از اولين نكات آگاهي دقيق بر نقش موضع اتصال و نوع مقدار تنش هاي اعمال شده بر آن است. با دانستن نوع نيرو و جهت آن مي توان طرح اتصال صحيح در محل مناسب را براي جوش مشخص كرد تا بيشترين نيرو را تحمل كند و يا با بيان ديگر تمركز تنش بر روي جوش بوجود نيايد.
طراحي اتصال بر حسب نوع تنش هاي يك سويي و يا چند سويي و همچنين اعمال نيروهاي استاتيكي يا ديناميكي ، متفاوت است .[1]
حجم يا اندازه جوش و ميزان تحمل يا مقاومت آن تحت نيروهاي اعمال شده موضوع ديگري است كه در طراحي جوش در نظر گرفته مي شود . البته در اينجا محاسبات با توجه به سالم بودن جوش انجام مي گيرد . بطور كلي موضوعات طراحي جوش شامل طرح اتصال ، موضع اتصال اندازه جوش و استحكام اتصال است.
عواملي كه در طراحي جوش لازم است در نظر گرفته شوند عبارتند از:
1- طرح بايد مقاومت مورد نظر را تامين كند . طراحي بيش از حدود خواسته شده به معني صرف مواد ، انرژي و هزينه بالاتر است
2- فاكتورهاي ايمني يا ضريب اطمينان در طرح بايد معقول و به اندازه اي باشد تا همه پيش آمدهاي احتمالي را تحمل كند . استفاده از فاكتورهاي ايمني خيلي زياد نيز موجب بالا بردن هزينه توليد قطعه مي شود
3- ظاهر موضع جوش ، نيز ممكن است در انتخاب روش جوشكاري تاثير گذارد ، اما طبيعي است كه هنگاميكه اين موضع در معرض ديد نبوده و در پشت قسمتي پنهان شده و يا اصولا اهميت نداشته باشد مي تواند موجب كاهش هزينه شود
4- هر جا كه امكان دارد از فولادهاي معمولي استفاده شود چون داراي مشكلات كمتري در جوشكاري است . بجز در موارديكه قطعه بايد پاسخگوي خواصي ويژه باشد يا با استفاده از فولادهاي آلياژي مقاوم ، مي توان موجب تقليل وزن و در مجموع كاهش هزينه شد
5- سبكي وزن : چون وزن بيشتر قطعه به معني هزينه بيشتر با توجه به دست يابي به دقت و خواسته مورد نظر بايد سعي در كاهش وزن اجزا قطعه و حتي موضع جوش شد
6- در بعضي مواقع جوشكاري بر روي قطعات ضخيم و سنگين با مشكلات بيشتري نيز روبرو است
7- رعايت حدود استاندارد ، در صورت امكان اندازه ها و شكل استاندارد تصريح شود
8- عمليات حرارتي مورد نياز
طرح اتصال
طرح اتصال بطور قابل ملاحظه اي متأثر از هزينه آماده سازي لبه مورد اتصال ، امكان دسترسي به درز جوش, قابليت پذيرش براي قطعه طرح شده ، نوع نيروهاي اعمال شده بر جوش و فرآيند جوشكاري است. طرح يا شكل اصلي اتصال كه براي فرآيند جوشكاري با الكترود دستي ، قوس با گاز محافظ و قوس زير پودري پذيرفته شده جوش لب به لب يا سر به سر شكاف دار و جوش نبشي است . كه هر كدام به چندين نوع تفكيك شده تا نياز خدمت هاي مختلف را فراهم كند . اين انواع در زير آمده است.
1- طرح اتصال لب به لب (Butt)
طرح اتصال لب به لب تخت يا مقطع با زاويه قائمه ترجيحا براي قطعاتي كه ضخامت آنها 10mm يا كمتر هستند و در جائيكه ذوب كامل با مقاومت حد بالا نياز است مناسب باشد . اتصال بطور قابل توجهي تحت نيروهاي استاتيكي كششي قوي بوده ولي هنگاميكه كشش در اثر خميده شدن و تمركز تنش در ريشه جوش است, مناسب نيست . هرگز نبايد اين طرح را در مواقعيكه اتصال تحت نيروهاي خستگي زا يا نيروهاي ضربه اي بويژه در درجات پايين قرار دارد بكار رود . يكي از مزاياي مهم اين طرح كم خرج و ساده بودن آماده سازي لبه ها بوده و كافي است لبه هاي تخت بطور مستقيم و قابل انطباق بر رويهم باشند.
طرح اتصال لب به لب يا پخ جناقي يكطرفه يا V براي ورقه هاي 10mm و ضخامت بيشتر استفاده مي شود . مخارج پخ سازي لبه هاي مورد اتصال بيشتر و مقدار فلز پر كننده بيشتري هم لازم دارد . زاويه پخ ، عمق ريشه پخ نشده و فاصله ريشه در شرايط مختلف قابل تغيير هستند . اتصال تحت نيروهاي استاتيكي قوي اما همانند طرح اتصال قبلي براي تنش هاي كششي ناشي از خمش مناسب نيستند چون تحت اين چنين نيروهاي تمركز تنش در ريشه جوش ايجاد مي شود.
طرح اتصال لب به لب با پخ جناقي دو طرفه يا X بهترين طرح براي همه وضعيت هاي نيرو مي باشد كه اغلب اختصاص به قطعات سنگين تر از موارد پخ جناقي يكطرفه دارد . براي استحكام ، ماكزيمم ، نفوذ ذوب بايد در دو طرف كامل بوده و يا بيان ديگر ذوب در دو طرف بهمديگر برسند . هزينه آماده سازي لبه ها بيشتر از پخ جناقي يكطرفه است اما فلز جوش كمتري لازم است. براي پايين نگهداشتن ميزان پيچيدگي زاويه اي بهتر است فلز جوش را متناوبا در دو طرف پخ رسوب داد و از پر كردن كامل يا رسوب چندين پاس در يكطرف و سپس شروع عمليات در طرف ديگر اجتناب شود.
طرح اتصال لب به لب لاله اي يا يكطرفه U يكطرفه همه حالت هاي نيرو را تحمل كرده و غالبا براي مواردي كه كيفيت بالايي مورد نظر باشد استفاده مي كنند . بالاترين كاربرد اين اتصال ورق هاي 18mm است.
طرح اتصال لب به لب لاله اي دو طرفه براي ورق هاي 18mm يا بزرگتر و براي همه حالتهاي نيروهاي معمولي متناسب است . اگر چه آماده سازي و پخ سازي لبه ها داراي بيشترين هزينه نسبت به انواع ديگر است اما فلز جوش كمتري نسبت به U يكطرف و V مصرف مي شود.
در اينجا لازم به تذكر است كه طرحهاي ديگر نيز براي اتصال سربه سر يا لب به لب وجود دارد كه از اهميت كمتري برخوردار بوده و در موارد خاص استفاده مي شود منجمله پخ كردن يكي از لبه هاي دو جز مورد اتصال كه به پخ J يا K يا Y مشخص مي شوند. نكته ديگر گاهي محدوديت جوشكاري در يكطرف كار وجود دارد ضمناً دست يابي به نفوذ كامل جوش نيز ضروري است در اين مواقع از سيستم هاي مختلف پشت بند Backing systems استفاده مي كنند . پشت بندها مي توانند از انواع سراميكي ، مسي ، فولادي ثابت يا قابل برداشت باشند در اين مورد قبلا توضيح داده شده است.
طرح اتصال سپري (T-joint)
طرح اتصال سپري يا T با مقطع تخت يا مربعي Square Tee نياز به جوش نبشي دارد كه مي تواند در يكطرف يا دو طرف قطعه كار انجام شود . اين طرح براي قطعات سبك تا بطور قابل ملاحظه اي ضخيم در جائيكه نيروي اعمال شده ايجاد تنش برشي طولي مي كند استفاده مي شود . چون توزيع تنش هاي برشي يكنواخت نيست بايد در استثنا نمودن اين طرح اتصال در مواردي كه تحت ضربه هاي شديد يا نيروي عرضي سنگين قرار مي گيرد دقت كرد . براي دست يابي به ماكزيمم مقاومت نياز به مقدار فلز جوش قابل توجه است.
سپري گونيا که براي ضخامتهاي کمتر از 20- 10 ميليمتر مناسب است.
- طرح اتصال سپري نيم جناقي يا V يكطرفه ممكن است در برابر نيروهاي شديدتري نسبت به حالت قبل مقاومت كند چون تنش ها بهتر توزيع مي شوند . عموما براي ورق هاي اينچ با ضخامت كمتر در جائيكه جوشكاري فقط از يكطرف امكان پذير است بكار مي رود
- طرح اتصال سپري نيم جناقي يا V دوطرفه براي جائيكه نيروهاي سنگين و هر دو نوع تنش طولي و عرضي اعمال شده همين طور امكان جوشكاري در دو طرف وجود دارد بكار مي رود
- طرح اتصال سپري نيم لاله يا J يكطرفه بر روي ورق هاي 25.4mm يا بيشتر و در جائيكه جوشكاري محدود به يكطرف است بكار مي رود . اين طرح بويژه جائيكه نيروهاي شديد و جدي مطرح است مناسب مي باشد
- طرح اتصال سپري نيم لاله اي يا J دوطرفه مناسب براي ورق هاي سنگين 37.5mm به بالا و در جائيكه نيروهاي شديد و غير معمول اعمال مي شود مناسب است . وضعيت اتصال بايد اجازه جوشكاري در دوطرف را بدهد
طرح اتصال لب رويهم (Over Lap)
طرح اتصال لب رويهم نبشي يكطرفه و طرح اتصال لب رويهم نبشي دوطرفه دو نوع طرح اتصال است كه بطور قابل ملاحظه اي در جوشكاري استفاده مي شود . اتصال لب رويهم نبشي دو طرفه مي تواند تحت نيروهاي شديد بيشتري مقاومت كند . اين طرح ها در لحيم كاري نرم و سخت و جوشهاي مقاومتي كاربرد فراوان دارد.
طرح اتصال گوشه اي (Fillet)
- طرح اتصال گوشه اي بسته اي ترجيحا براي جوشكاري ورق هاي نمره 12 يا نازك تر مناسب است . دست يابي به عمق نفوذ كامل مشكل بوده و براي نيروهاي متوسط قابل استفاده است.
- طرح اتصال گوشه اي نيم باز معمولا بيشتر براي ورق هاي سنگين تر از نمره 12 قابل پذيرش است . نفوذ بهتر از گوشه اي بسته خواهد آمد .
- طرح اتصال گوشه اي كاملا بازدر جائي استفاده مي شود كه جوشكاري مي تواند از دو طرف انجام شود . ورق در همه ضخامت هاي با اين طرح قابل اتصال دادن است . اين نوع اتصال قوي بوده و مي تواند نيروهاي سنگين را تحمل كند . اين طرح همانطور براي نيروهاي خستگي زا يا ضربه اي قابل كاربرد است زيرا توزيع تنش خوبي در اين طرح انجام مي گيرد . در اتصال گوشه اي يا نبشي هم غالبا پخ كردن يا هر دو جز مورد اتصال متدادل است.
طرح اتصال لبه اي (Edge)
طرح اتصال لبه اي براي ورق هاي نازك 6.4mm و ضخامت كمتر بكار مي رود و مي توان بدون استفاده از مفتول پر كننده عمليات جوشكاري را انجام داد . اين طرح براي جوشكاري با شعله و TIG بدون استفاده از مفتول مناسب است.
گاهي اوقات طرح اتصال داراي آنچنان شكلي است كه نياز به پخ سازي جداگانه لبه ها نيست نظير اتصال طولي اشكال استوانه اي يا استوانه اي به سطح.
همانطور كه اشاره شد در انتخاب طرح مناسب براي اتصال فاكتورهاي تقليل هزينه آماده سازي لبه ها و اتصال و دست يابي به استحكام مورد نظر ، ضخامت قطعه كار و امكانات اجرايي رسوب دادن فلز جوش مطرح است.
بدون شك لبه هاي بدون پخ يا مقطع مربع از نظر هزينه آماده سازي لبه ها و جوشكاري پايين تر است اما لازم است تاكيد شود كه اين طرح اغلب براي ورق هاي سبك و ضخامت پايين مناسب است . هر چند پخ كردن لبه ها موجب افزايش هزينه اتصال مي شود اما براي اتصال ورق هاي ضخيم و سنگين و دست يابي به نفوذ كامل پخ سازي مناسب ضروري است در غير اينصورت نفوذ كامل كامل غير ممكن بوده و جوش با نفوذ ناقص ضعيف خواهد بود . يكي از روشهاي متداول براي دست يابي به بهترين نتايج با كمترين هزينه انتخاب شكاف ريشه اي باز و پخ كردن لبه ها با زاويه معيني كه نياز به كمترين مقدار فلز پر كننده باشد است . ميزان زاويه شكاف اغلب متاثر از امكانات اجرائي جوشكاري و تسهيلات مربوطه است . بعنوان مثال وضعيت و موقعيت اجراي مورد جوش نسبت به يكديگر ممكن است طوري باشد كه جوشكاري فقط از يكطرف امكان پذير باشد . در زير شکلهاي آمده است که نحوه محاسبه تنشهاي وارده بر جوش را در حالتهاي مختلف نشان ميدهد.
هنگامي كه ضخامت فلز پايه از 6mm بيشتر مي شود براي آنكه نفوذ جوش به صورت كامل تا ريشه جوش انجام شود لازم است لبه هاي مورد جوشكاري پخ سازي شود . هر چه ضخامت فلز پايه بيشتر شود نياز به لبه سازي و پخ سازي بيشتر مي شود . به طور كلي جوش ها را به دو دسته عمده مي توان تقسيم بندي كرد:
- جوش لب به لب
- جوش جناقي
هر دو نوع اين جوشها هنگامي كه ضخامت قطعه از حدي بيشتر مي شود بايد لبه سازي گردد. براي آنكه نفوذ جوش مناسب باشد لازم است از طراحي اجرا جوش و شكل لبه سازي دقت هاي خاصي انجام گردد. زاويه پخ سازي يكي از مواردي كه در اين حالت از اهميت برخوردار است . علاوه بر زاويه پخ سازي فاصله ريشه جوش و اندازه لبه ريشه در نفوذ جوش اهميت دارد .
هدف از لبه سازي آن است كه جوش به صورت كامل نفوذ كند . و اصطلاحا جوش با نفوذ كامل را full penetration joint گويند . در همه جا لازم نيست جوش اجرا شده نفوذ كامل داشته باشد . در جوش هايي كه با حالت استاتيك دائم دارد از جوش با نفوذ ناقص يا جزئي مي توان استفاده كرد. partion penetration joint بر روي نقش هاي فني ساخت جوش هايي كه تحت بارهاي ديناميك و استاتيك قرار مي گيرند با علامت (fpj) و جوشهايي كه تحت بار فقط استاتيك قرار مي گيرد مي توانند نفوذ كامل نداشته باشند و با علامت(ppj) مشخص مي شوند براي مشخص كردن جوشها بر روي نقش ها از علائم خاص به صورت استاندارد استفاده مي شود.
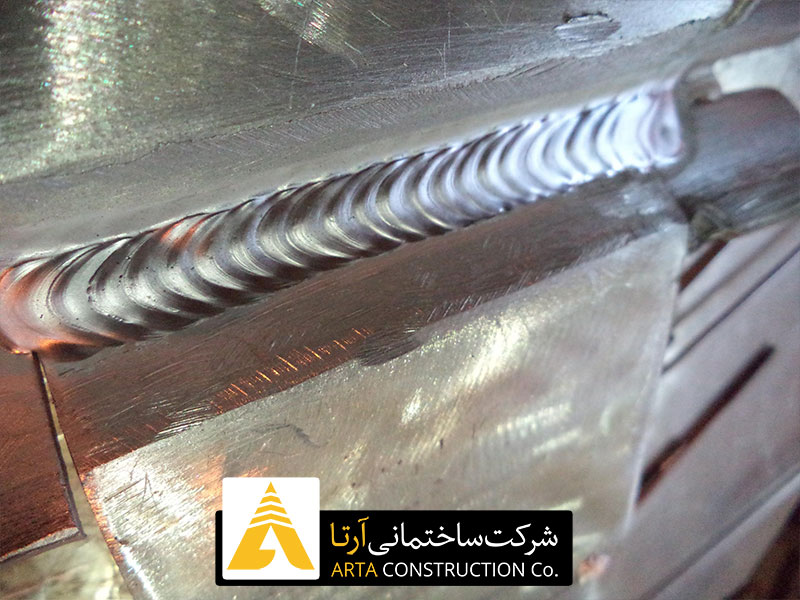
روشهاي پخ سازي :
پخ سازي از روشهاي مختلفي در صنعت انجام مي شود كه مهمترين آنها عبارتند از:
1- پخ سازي با شعله اكسي استيلن با استفاده از تورچ هاي اتوماتيك
2- پخ سازي با استفاده از ماشين هاي پخ زني مكانيكي مانند گيوتين ها و دستگاههاي براده برداري (پليسه برداري)
3- پخ سازي با استفاده از تورچ پلاسما و ساير روشهاي برش مانند ليزر .
کار عملي و مشاهدات آزمايشگاهي
هدف آزمايش :
بررسي کيفيت و نفوذ جوش اجرا شده در حالتهاي پخ زده شده و بدون پخ زدن.
تجهيزات آزمايش:
1- ماشين پخ زني از نوع براده برداري
2- دستگاه رکتيفاير جوشکاري
3- ورق فولاد ساده کربني از جنس St37 به ضخامت 8-3 ميليمتر
4- الکترود E6013 به قطر 25/3 ميليمتر
5- لباس کار, دستکش, انبر جوشکاري, چکش گل زن, برس سيمي, عينک يا ماسک جوشکاري.
روش آزمون
دستگاه مورد استفاده در اين آزمايش از نوع مکانيکي و براده برداري است که قابليت تنظيم زاويه از 5/22 تا 55 درجه را دارد. اين دستگاه قابليت پخ زني ورقهاي فولادي تا ضخامت10 ميليمتر و ورقهاي آلومينيومي تا ضخامت 38 ميليمتر را دارد ولي براي ورقهاي کمتر از 6 ميليمتر مناسب نمي باشد. دستگاه داراي يک فک متحرک و يک فک ثابت ميباشد که قطعهبين اين دو فک قرار گرفته و در طول فکها حرکت نموده و پخ زده ميشود. سرعت حرکت دستگاه يا ميباشد. ضخامت پخ ماکزيمم براي فولاد 10 ميليمتر و براي آلومينيوم 38 ميليمتر است. عرض پخ ماکزيم 18 ميلمتر و عمق پخ ماکزيمم 15 ميليمتر است.
در اين آزمايش از ورق فولاد ساده کربني St37 به ضخامت 6 ميليمتر استفاده ميشود که با زاويه 5/37 درجه پخ زني ميشود (در اينصورت زاويه پخ زني 75 درجه است) و سپس با روش جوشکاري قوس الکتريک دستي جوش داده ميشود. همچنين يک قطعه از همين فولاد و با همين ضخامت بدون پخ زني جوشکاري ميشود و کيفيت جوشکاري هر دو مورد با هم مقايسه ميگردد. براي جوشکاري از الکترود E6013 و به ضخامت 25/3 ميليمتر استفاده ميشود و سپس جوش مقطع زده شده و با بررسي متالوگرافي روي آن صورت ميگيرد.
مشاهدات
1- جوشکاري همراه با پخ زني
ابتدا لازم است قبل از جوشکاري پشت خط جوش يک پشت بند مسي قرار داده تا قطعه در حين جوشکاري سوراخ نشود. علت انتخاب پشت بند مسي اين است که بعد از جوشکاري به راحتي کنده ميشود.
شدت جريان دستگاه را روي 115 آمپر تنظيم ميشود و با قطبيت مثبت DCEP جوشکاري ميگردد. بايد دانست که در اين حالت زاويه پخ زني 75 درجه, فاصله ريشه و اندازه لبه ريشه صفر ميباشد.
Groove Angle = 75º , Root Opening = 0 , Root Face = 0
مشاهده ميگردد که در پاس اول جوشکاري نفوذ فوق العاده خوب است و از پشت خط جوش بيرون زده شده است. بعد از جوشکاري پاس اول بايد با چکش گل زن گل جوش زده شود چون در غير اينصورت در جوشکاري پاس دوم مشکل ساز ميشود و ايجاد حفره مي نمايد. به طور کلي هرچه زاويه پخ زني بيشتر باشد عمق نفوذ بيشتر است و مقدار مصرف الکترود نيز بيشتر ميشود.
2- جوشکاري بدون پخ زني
شدت جريان و قطبيت مانند حالت قبل است. در اين حالت نفوذ کامل نميباشد و از نظر استاندارد رد است و فقط براي جوشهايي که تحت بار استاتيک هستند مناسب است.
متالوگرافي مقطع جوش
براي متالوگرافي ابتدا مراحل آماده سازي سطح شامل برش, سوهان, سنباده و پوليش انجام ميشود و سپس قطعات از نضر عمق نفوذ جوش مورد بررسي قرار ميگيرند. شکل زير نشان دهنده مقطع برش قطعه اي است که بدون پخ زني جوشکاري شده است. همانطور که از شکل مشخص است نفوذ جوش در بين درز جوش کافي نبوده و اين باعث ايجاد عيب در قطعه ميگردد.
نتيجه گيري
1- طرح اتصال بطور قابل ملاحظه اي متأثر از هزينه آماده سازي لبه مورد اتصال ، امكان دسترسي به درز جوش, قابليت پذيرش براي قطعه طرح شده ، نوع نيروهاي اعمال شده بر جوش و فرآيند جوشكاري است .
2- طرح اتصال لب به لب تخت يا مقطع با زاويه قائمه ترجيحا براي قطعاتي كه ضخامت آنها 10mm يا كمتر هستند و در جائيكه ذوب كامل با مقاومت حد بالا نياز است مناسب باشد.
3- گاهي محدوديت جوشكاري در يكطرف كار وجود دارد ضمناً دست يابي به نفوذ كامل جوش نيز ضروري است در اين مواقع از سيستم هاي مختلف پشت بند Backing systems استفاده مي كنند . پشت بندها مي توانند از انواع سراميكي ، مسي ، فولادي ثابت يا قابل برداشت باشند.
4- طرح اتصال سپري براي قطعات سبك تا بطور قابل ملاحظه اي ضخيم در جائيكه نيروي اعمال شده ايجاد تنش برشي طولي مي كند استفاده مي شود.
5- طرح اتصال لب رويهم نبشي يكطرفه و طرح اتصال لب رويهم نبشي دوطرفه دو نوع طرح اتصال است كه مي توانند تحت نيروهاي شديد بيشتري مقاومت كنند . اين طرح ها در لحيم كاري نرم و سخت و جوشهاي مقاومتي كاربرد فراوان دارند .
6- طرح اتصال لبه اي براي ورق هاي نازك 6.4mm و ضخامت كمتر بكار مي رود و مي توان بدون استفاده از مفتول پر كننده عمليات جوشكاري را انجام داد . اين طرح براي جوشكاري با شعله و TIG بدون استفاده از مفتول مناسب است.
7- بدون شك لبه هاي بدون پخ يا مقطع مربع از نظر هزينه آماده سازي لبه ها و جوشكاري پايين تر است اما لازم است تاكيد شود كه اين طرح اغلب براي ورق هاي سبك و ضخامت پايين مناسب است.
منابع و مراجع
1- اميرحسين کوکبي, تکنولوژي جوشکاري, نشر آزاده و جامعه ريخته گران ايران, 1374
2- جزوه درسي آزمايشگاه جوشکاري فلزات , دکتر مهرداد عباسي